Od krakowskiej (głównej) siedziby ASTOR dzieli mój dom kilka przecznic, wywiad udało się (w końcu!) przeprowadzić prawie dwa lata od momentu, w którym zaczęłam pisać dla MamStartup. Najwyższy czas!
ASTOR to jedna z najważniejszych (i najdłużej działających, od 1987 roku) polskich firm automatyzujących zakłady produkcyjne w naszym kraju. Na swoim koncie mają ponad 50 tysięcy sprzedanych systemów dot. automatyzacji, robotyzacji i cyfryzacji produkcji, posiadają własne Centrum Badań i Rozwoju, tworzą własne rozwiązania, są jedynym dystrybutorem robotów Kawasaki w Polsce. Od kilku lat zaangażowani w budowanie współpracy dużych firm przemysłowych ze startupami w ramach programu KPT ScaleUp. Jeżeli będziecie w Krakowie, koniecznie odwiedźcie jeden z showroomów ich Fabryki Przyszłości (“trasy” opracowane i dla inżynierów i dla maluchów).
Prezesa ASTOR, a wcześniej dyrektora ds. Przemysłu 4.0, Jarosława Gracela, zapytałam o to czym żył polski przemysł w kończącym się roku, a także o to, jakimi technologiami polskie firmy przemysłowe będą najbardziej zainteresowane w nadchodzących roku. Rozmawialiśmy również o postępach we wdrażaniu mikrofabryk.
Jakim jednym słowem można najlepiej podsumować to, co najmocniej kształtowało rozwój przemysłu w 2021 roku?
Słowem roku w przemyśle były zdecydowanie łańcuchy dostaw, a raczej praca nad wielkimi zaburzeniami, które pojawiły się w tym obszarze. Czy będę miał towar w ilości, którą zamówiłem? Kiedy przyjdzie? A jak już go dostanę, to w jakiej ilości i jakie będą koszty jego transportu? Bo jeżeli te ostatnie mocno wzrosną, to będę musiał zmienić cenę dla klienta.
Małe firmy w mniejszym stopniu odczuły te zaburzenia, o tym dlaczego, za chwilę. Tak naprawdę im większa firma, tym większy problem: po pierwsze mają dużo więcej zamówień, a po drugie dużo bardziej wymagających klientów – oni nie poczekają kilku dni na dostawę, są dużo mniej elastyczni. Dlatego w tym roku duże firmy inwestowały mocno w cyfryzację łańcuchów dostaw, aby móc monitorować to, jakie dostawy przyjdą, jakie mają alternatywy. To są wyzwania dla dużych firm.
Małym firmom było oczywiście trudniej negocjować czas dostaw itd., ale z drugiej strony ich niewielki rozmiar miał swoje korzyści, w szczególności mam tutaj na myśli ich elastyczność. Jak nie kupię tutaj, to kupię z innego miejsca; na przykład dużo szybciej potrafią zmienić formę dostawy – z kontenera, który płynie drogą morską, na pociąg lub samolot, bo ilości, które zamawia są niewielkie – dużo łatwiej zorganizować więc zmiany i “znaleźć miejsce” na ich towar w alternatywnym środku transportu. Dlatego moim zdaniem kluczowe wyzwania małych firm w roku 2021 nie leżały w zaburzeniach łańcuchów dostaw, choć oczywiście były także problemem. Główne zadanie mniejszych przedsiębiorstw w mijającym roku to kompletowanie kadry: wyłuskanie z rynku zarówno pracowników fizycznych, jak i specjalistów-inżynierów. Z jednej strony, gdy nie ma pracowników na rynku, rozwiązaniem jest zastępowanie ich robotami/automatyzacją procesów, ale z drugiej strony, jak to robić, gdy brakuje również pracowników wykwalifikowanych?
Na którą stronę przechyliła się więc szala w tym roku? Gorączkowych poszukiwań pracowników czy robotyzacji?
Skupiają się na robotyzacji i to jest ogromna zmiana, która nastąpiła w ciągu ostatnich dwóch lat, na to nałożyło się kilka różnych czynników. Ciągły spadek cen robotów w okresie ostatnich piętnastu lat. Tanie kredyty. Różnego rodzaju wsparcie publiczne na unowocześnianie produkcji. I to, o czym już wspominałem, czyli braki kadrowe. Małe firmy kupują masowo roboty i widzę, że to jest naprawdę przełomowy rok.
Jaki typ robotów? Bardziej zastępujące pracownika na jego stanowisku pracy czy optymalizujące procesy, przyspieszające i wzmacniające analizę danych?
Z naszych danych sprzedażowych wynika, że są to głównie roboty przemysłowe, szczególnie roboty spawalnicze, a to ze względu na to, że mamy w Polsce bardzo duży niedobór spawaczy. Na drugim miejscu pod względem zamówień plasują się roboty pakujące i do paletyzacji. Trzecie miejsce na podium zajmują maszyny zastępujące człowieka przy prasach – tu wysokie zainteresowanie ze względu na niskie bezpieczeństwo tej pracy dla człowieka – wypadki towarzyszące jej obsłudze. Te rodzaje robotów są w top trzy rodzajów robotów, które kupują małe firmy produkcyjne w Polsce.
Mówimy o małych firmach, ale doprecyzujmy to sformułowanie. Jaka jest graniczna liczba zatrudnionych, poniżej której nie opłaca się wdrożyć w produkcji robota?
Mówię tutaj już o naprawdę niewielkich firmach – nawet tych zatrudniających 10-15 osób (które mają – warunek konieczny – mocno powtarzalne procesy; w małej firmie może to być np. produkcja łopat). Nawet tym przedsiębiorcom robota opłaca się kupić z dwóch powodów: pierwszy – malejące od piętnastu lat ceny robotów, drugi – mocno rosnące pensje specjalistów. W tym momencie koszt stanowiska spawacza jest tak samo wysoki, jak cena robota spawalniczego. Koszt stanowiska spawalniczego to 500 000 złotych, niemała kwota. Ale zestawmy to z pensją pracownika: doświadczonemu spawaczowi trzeba zapłacić 10 000 złotych brutto miesięcznie, do tego trzeba dodać koszty dla firmy w wysokości 3 000 złotych, tak więc przez rok koszt jego zatrudnienia to 156 000 złotych. W sytuacji więc, gdy pracujemy na jedną zmianę, zakup robota zwróci się nam już po trzech latach, a jeżeli zakład pracuje na dwie zmiany, to w półtora roku. Kolejna korzyść jest taka, że robot można wziąć – w odróżnieniu od pracownika – w leasing – na dwa, trzy lata, to nie musi być inwestycja na całe życie.
W odróżnieniu od robotów, wdrożenie oprogramowania do analizy danych czy cyfryzacja zarządzania procesami, to są już wyższe koszty i na tego typu rozwiązania mogą sobie pozwolić w tym momencie tylko duże firmy.
Jak mocny wpływ na decyzje firm będzie miała ulga na robotyzację? Czy rok 2022 będzie rokiem masowej robotyzacji polskich firm?
Porównując ten przepis do działań prowadzonych w Japonii w latach 50. i 60. XX wieku, można liczyć na bardzo pozytywny efekt ulgi na robotyzację. Tam państwo dopłacało połowę ceny zakupu nowych technologii i to spowodowało gwałtowną zmianę struktury firm japońskich. W Polsce potrzebujemy dokładnie tego samego efektu. W tym momencie tylko 25% polskich firm wdraża rozwiązania automatyzacji i robotyzacji (raport Siemens), a celem dla naszej gospodarki powinno być odwrócenie tej sytuacji – żebyśmy za 10 lat mieli 25% firm, które nie wdrożyły rozwiązań przemysłu 4.0. Ulga na robotyzację spowoduje, że wiele firm odważy się i zainwestuje w swojego pierwszego roboty. Gdy zobaczą już, jakie korzyści to niesie, to pójdzie lawinowo, ale ulgi na zakup są kluczowe, żeby ruszyć tę zmianę.
Pamiętajmy, że ulgę na robotyzację można przeznaczyć nie tylko na zakup robotów produkcyjnych czy mobilnych, ale również na cyfryzację zarządzania fabryką i w ten sposób optymalizować koszty działania firmy.
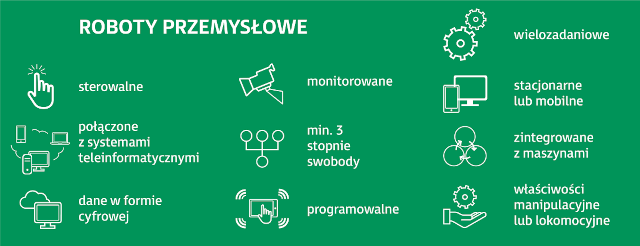
O tym, że dofinansowanie zakupu robotów w postaci ulgi przyniesie wymierne korzyści firmom, mówił na łamach naszego magazynu [Biznes i Produkcja, przyp. red. MS] dyrektor operacyjny ASTOR, Andrzej Garbacki: “Państwo decyduje się na taką inwestycję, bo wie, że po zastosowaniu robotyzacji, dochodowość firm znacznie wzrośnie. Inwestycja państwa w ulgę zwróci się w podatku dochodowym już w pierwszym roku po zakończeniu odliczeń. Jestem głęboko przekonany, że tak się stanie”. I dodał argument za swoją tezą wskazując na przykład silnie zrobotyzowanego przemysłu naszego sąsiada zza Odry: “Na Zachodzie jest 7 razy więcej robotów na jednego pracownika. Co za tym idzie przy 2-3 krotnie wyższych pensjach w Niemczech, te firmy dalej są konkurencyjne, dalej na rynku międzynarodowym potrafią istnieć, sprzedawać, rozwijać się pomimo, że mają znacznie wyższe koszty pracy, obciążenia podatkowe”.
Mikrofabryki to bardzo obiecujące rozwiązanie dla startupów, ponieważ dają możliwość wyprodukowania swojego produktu na własnych warunkach, a przede wszystkim nie wymagają tak dużych nakładów finansowych, jak budowa tradycyjnego zakładu produkcyjnego – są w zasięgu niewielkich, początkujących firm. Na ile w tym momencie realna jest w Polsce budowa własnej mikrofabryki przez startup/niewielką firmę?
Koncepcja mikrofabryk nie jest jeszcze rozpowszechniona, większość z tego typu rozwiązań jest jeszcze na etapie badań i rozwoju. To, co jest głównie rozwijane, to mobilne, modułowe fabryki, które można przenosić z miejsca na miejsce. Są w Polsce już przykłady takich mikrofabryk, np. minifabryka przy każdym budowanym moście, która na miejscu spawa i obrabia części metalowe. W Polsce taką koncepcję rozwija SKANSKA ze swoimi flying factories. Cela spawalnicza może być również przykładem takiej mikrofabryki, bo można ją w kilka godzin rozłożyć i przewieźć w inne miejsce.
–
Mikrofabryki odpowiedzią na zaburzenia dostaw?
Wskazanie przez prezesa ASTOR problemu zaburzeń łańcuchów dostaw, jako najważniejszego wyzwania przemysłu w mijającym roku, kieruje uwagę w stronę świeżej koncepcji mikrofabryk. Dobrym przykładem jej wdrożenia jest brytyjski startup Arrival produkujący samochody elektryczne “na miejscu” – na obrzeżach miast z największym potencjalnym rynkiem zbytu. Taki model biznesowy jest możliwy dzięki niewielkiej (“mikro”) skali fabryk – tanich, niewielkich powierzchniowo fabryk można wybudować więcej, niż kilkusethektarowych gigantów, a dzięki temu blisko odbiorców. W dzisiejszych czasach, gdy globalne łańcuchy dostaw uległy tak mocnym zaburzeniom, kierowanie się w stronę lokalnej produkcji, jest jak najbardziej obiecującą wizją.
W naszym tekście, Startupy mogą produkować samochody, w realizacji celu pomagają mikrofabryki, pisaliśmy również o innych korzyściach, które potencjalnie mogą przynieść wytwórcom mikrofabryki, np. o mniejszych problemach ze znalezieniem pracowników, gdy trzeba znaleźć ich jednorazowo nie stu, ale kilkunastu. A problem ze znalezieniem odpowiedniej kadry, to od kilku lat jedna z największych bolączek firm produkcyjnych w naszym kraju.